Have you ever stumbled upon an uneven sidewalk or tripped on an unlevel driveway? The culprit behind these treacherous surfaces might be due to soil settling and erosion. In this article, we’ll delve into two popular solutions for these pesky problems: mudjacking and foam leveling. By the end, you’ll have a clear understanding of these methods, helping you make an informed decision for your property.
Mudjacking: A Tried-and-True Solution
Mudjacking, also known as slabjacking or grout pumping, has been a reliable method for raising and leveling sunken concrete surfaces for decades.
Mudjacking: A Tried-and-True Solution
Mudjacking, also known as slabjacking or grout pumping, has been a trusted and reliable method for raising and leveling sunken concrete surfaces for decades. This technique is commonly used for fixing uneven sidewalks, driveways, and patios.
The Mudjacking Process
Mudjacking is a relatively straightforward process that involves the following steps:
- Drilling small holes into the sunken concrete slab: Technicians strategically drill holes, usually about 1-2 inches in diameter, through the sunken concrete slab to access the voids beneath.
- Pumping a mixture of water, soil, and cement (called slurry) through these holes: A specialized pump is used to inject the slurry, which consists of water, soil, and cement, into the voids under the slab.
- The slurry fills the voids beneath the slab, lifting it to the desired level: As the slurry fills the empty spaces, it exerts pressure on the slab, gradually raising it to the desired level.
- Once the slab is level, the holes are filled and sealed, leaving a safe and even surface: After the slab has been lifted and leveled, the drilled holes are filled with a strong, fast-setting cement to blend with the surrounding surface, ensuring a smooth and even finish.
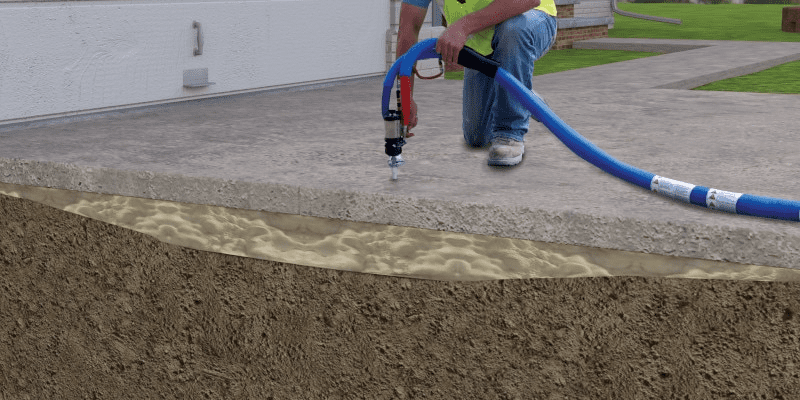
Advantages and Disadvantages of Mudjacking
Advantages:
- Cost-effective: Mudjacking is generally more affordable than foam leveling. The materials used in the slurry are less expensive, and the process is less labor-intensive, resulting in lower overall costs.
- Environmentally friendly: The slurry used in mudjacking is made from natural materials, which can be recycled or repurposed. This environmentally-conscious approach minimizes waste and makes mudjacking a more sustainable option.
- Proven track record: With decades of successful applications, mudjacking has proven to be an effective and reliable solution for raising and leveling sunken concrete surfaces.
Disadvantages:
- Aesthetics: Mudjacking requires drilling visible holes in the concrete, which can be an eyesore. Although the holes are filled and sealed after the process, they may still be noticeable on the surface.
- Heavier: The slurry used in mudjacking can add significant weight to the soil beneath the slab. Over time, this additional weight may cause further soil settlement and compaction, potentially leading to more issues in the future.
- Limited lift: Mudjacking may not provide adequate lift for extremely large or heavy slabs, which could require alternative methods or more extensive repairs.
- Longer cure time: The slurry used in mudjacking takes longer to set and cure than the materials used in foam leveling. This means that the repaired surface may not be ready for use as quickly as it would be with foam leveling.
With a more comprehensive understanding of the mudjacking process and its advantages and disadvantages, you can make a more informed decision about whether this tried-and-true solution is the right fit for your property’s needs.
Foam Leveling: A Modern Alternative
Foam leveling, also known as polyurethane foam injection or foam jacking, is a newer and more advanced method for raising and leveling concrete surfaces. This innovative technique has gained popularity in recent years due to its quick, efficient, and precise results.
The Foam Leveling Process
Foam leveling is a high-tech process that involves the following steps:
- Drilling small holes into the sunken concrete slab: Similar to mudjacking, technicians drill small holes, usually about 5/8-inch in diameter, into the sunken concrete slab to access the voids beneath.
- Injecting a two-part polyurethane foam through these holes: A specialized pump injects a two-part polyurethane foam into the voids beneath the slab. The foam components mix as they are injected, creating a chemical reaction that causes the foam to expand rapidly.
- The foam expands, filling voids and lifting the slab to the desired level: The expanding foam fills the empty spaces beneath the slab, exerting upward pressure and raising the slab to its original, level position.
- Once the slab is level, the holes are filled and sealed, providing a smooth and even surface: After the slab has been lifted and leveled, the drilled holes are filled with a strong, fast-setting cement that blends with the surrounding surface, ensuring a smooth and even finish.
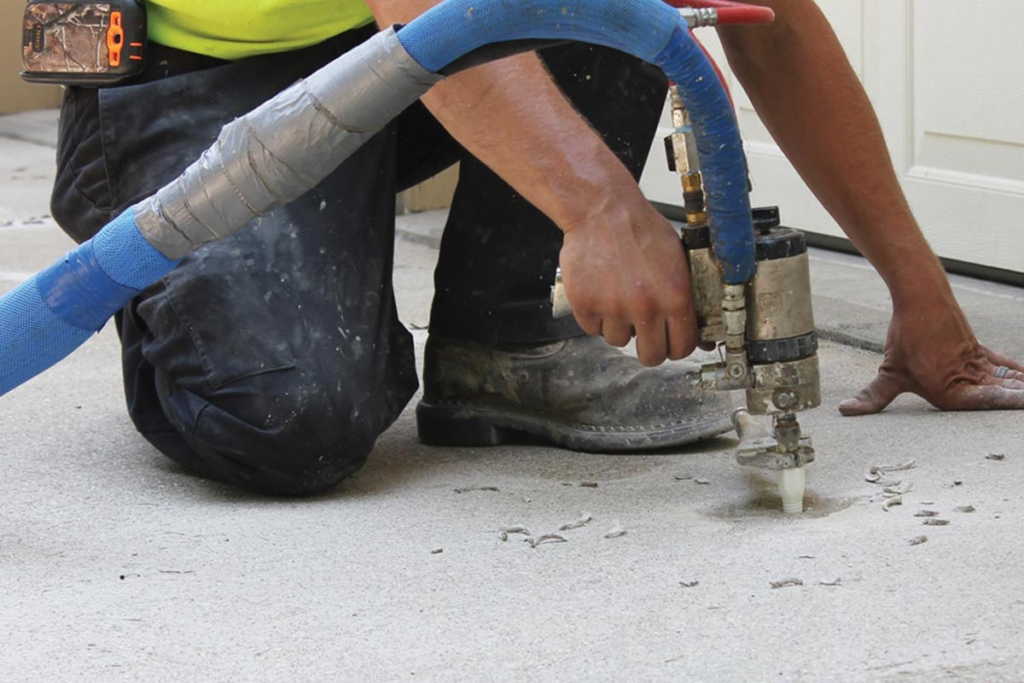
Advantages and Disadvantages of Foam Leveling
Advantages:
- Lightweight: The polyurethane foam used in foam leveling is significantly lighter than the mudjacking slurry, reducing the risk of further soil settlement and compaction.
- Speed: The foam cures quickly, often within minutes, allowing for faster project completion and minimal downtime. In many cases, the repaired surface is ready for use within hours of the foam leveling process.
- Precision: The expanding foam provides precise and even lifting, allowing for accurate leveling of the slab, even in complex or irregularly-shaped areas.
- Less invasive: The smaller holes required for foam leveling are less visible and less disruptive to the surrounding area, making it a more aesthetically pleasing option.
Disadvantages:
- Cost: Foam leveling is generally more expensive than mudjacking due to the higher cost of materials and the specialized equipment required for the process.
- Chemicals: The use of polyurethane foam raises concerns about potential environmental impacts, as it is a synthetic material derived from petroleum. However, many foam leveling companies use environmentally-friendly foam products with minimal environmental risks.
- Not suitable for all projects: Foam leveling may not be the best option for some situations, such as when there are concerns about the structural integrity of the slab, or when a more substantial repair is required.
Armed with a deeper understanding of the foam leveling process and its advantages and disadvantages, you can determine if this modern alternative is the ideal solution for addressing your property’s sunken concrete surfaces.
Making the Right Choice
Deciding between mudjacking and foam leveling depends on your specific needs and priorities. Consider factors like cost, aesthetics, and environmental impact. Additionally, consult with a professional foundation repair company, like Brothers Foundation Repair, to help you make an informed decision.
Conclusion
Both mudjacking and foam leveling are effective solutions for raising and leveling sunken concrete surfaces. By understanding the processes, advantages, and disadvantages of each method, you can confidently choose the best option for your property. Remember, a level surface isn’t just about appearance—it’s about safety and structural integrity too. So, don’t wait to address these issues; take action today and keep your property looking and functioning its best. Hire a reliable foundation repair contractor for your project – trust our expertise for exceptional results. Contact us today for a consultation!