Understanding Floating Slabs
Floating slab construction is a modern technique where a reinforced concrete slab is built directly on top of the ground, without the need for a foundation wall. This method provides excellent load-bearing capacity and insulation, making it suitable for various construction projects.
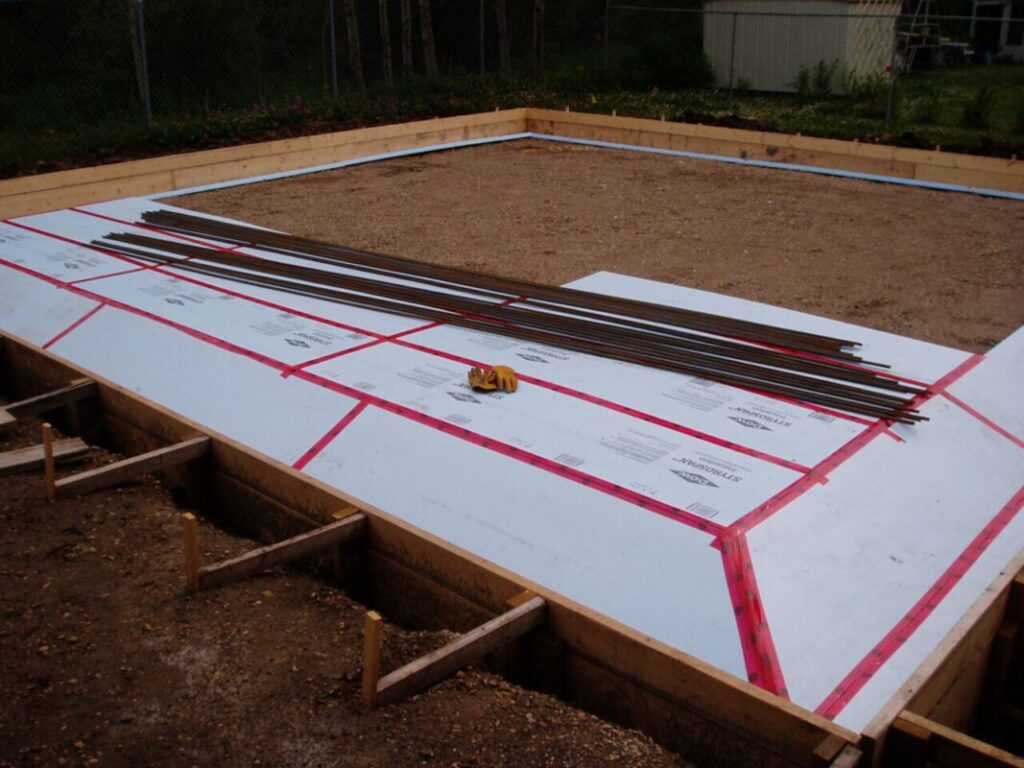
Applications of Floating Slab Construction
Floating slab construction can be used for a variety of applications, including:
- Garages and Sheds: A popular choice for garage and shed construction, floating slabs provide a cost-effective and durable foundation.
- Home Additions: Floating slabs are ideal for expanding existing structures, offering a seamless connection between the new and existing spaces.
- Industrial Buildings: The load-bearing capacity of floating slabs makes them perfect for heavy-duty industrial facilities.
- Commercial Buildings: Retail and office spaces can benefit from floating slab construction due to its energy-efficient and cost-saving features.
- Cabin Foundations: As a low-maintenance foundation option, floating slabs are perfect for remote or seasonal cabin locations.
Advantages of Floating Slab Construction
Floating slab construction offers numerous benefits over traditional foundation methods:
- Cost Savings: Floating slabs require less labor and material, resulting in a more affordable foundation solution.
- Efficiency: The simplified construction process enables faster project completion times.
- Insulation: The air gap between the ground and the slab offers improved thermal insulation, reducing energy consumption.
- Flexibility: The absence of a foundation wall allows for easy adjustments or expansions of the structure.
- Durability: Floating slabs provide excellent resistance to ground movement and frost heave, ensuring a long-lasting foundation.
Key Components of Floating Slab Systems
Floating slab systems typically consist of the following components:
- Reinforced Concrete Slab: The structural component that carries the load of the building.
- Vapor Barrier: A moisture-resistant layer placed between the slab and the ground to prevent moisture infiltration.
- Insulation Layer: Installed beneath the slab to improve thermal performance.
- Gravel Base: A compacted layer of gravel that provides a stable and level surface for the slab.
- Perimeter Grade Beam: A reinforced concrete beam around the edge of the slab that helps distribute loads and resist lateral soil pressure.
Floating Slab Construction Process
The construction process for floating slabs involves the following steps:
- Site Preparation: The area is cleared, leveled, and compacted to ensure a stable base.
- Gravel Base Installation: A layer of compacted gravel is placed to create a solid, level foundation.
- Insulation and Vapor Barrier Installation: These layers are added to enhance the slab’s thermal performance and prevent moisture infiltration.
- Formwork and Rebar Placement: Wooden forms are built to shape the slab, and steel rebar is installed for reinforcement.
- Concrete Pouring: The concrete is poured into the forms
- and carefully leveled to create a smooth and even surface. 6. Curing and Form Removal: The concrete is allowed to cure for a specific period, typically 7 to 28 days, before the forms are removed.
- Finishing Touches: Any required finishing work, such as sealing or painting, is completed to ensure the slab’s longevity and appearance.
- Maintenance and Repair of Floating Slabs
- Proper maintenance and timely repairs are essential for the longevity of floating slab systems:
- Regular Inspections: Periodically check for cracks, unevenness, or signs of moisture infiltration to detect potential issues early.
- Sealant Application: Applying a quality sealant helps protect the slab from moisture penetration, chemical exposure, and freeze-thaw cycles.
- Crack Repairs: Address cracks promptly to prevent further deterioration. Small cracks can be filled with an appropriate crack filler, while larger ones may require professional repair.
- Drainage Management: Ensure proper drainage around the slab to prevent water accumulation and potential damage.
- Cleaning: Regularly clean the slab surface to remove dirt, debris, and any potential contaminants that could harm the concrete.
Conclusion
Floating slab construction offers a range of advantages, including cost savings, efficiency, insulation, flexibility, and durability. With numerous applications in residential, commercial, and industrial settings, this innovative technique can enhance your construction projects. By partnering with Brothers Foundation & Concrete, you can benefit from our expertise in floating slab construction and ensure a high-quality, long-lasting foundation for your building. Restore the strength of your pier and beam house with professional repair services – schedule now!